昨今、よく聞く DX(デジタルトランスフォーメーション)とは、デジタル技術を活用し、企業が製品やサービスの変革を進めること、もしくはビジネスモデルそのものを変革し優位性を確立させるための活動のことです。製造業においても、企業の成長戦略における課題解決を助ける観点から DX への対応がますます重要になってきていると言えます。
人工知能の活用や、Minimal Fab(ミニマルファブ)の登場による技術革新など、近年の製造現場を取り巻く環境は大きく変化し続けています。そんな中、製造現場における「スマートファクトリー化」は、製造業における企業の DX を推進させる重要な一手と言えます。一方で、なかなかデジタル化が進まない、どこから導入すれば良いのかわからない、などその進め方に悩まれている製造現場の担当者や、経営責任者の方も多いかと思います。
そこでこの記事では、アイレットが出展した「スマートファクトリーJapan 2024 秋(以下、スマートファクトリー展)」を通じて見えてきた、製造現場で進む「スマートファクトリー化」の現在地とはどこなのかを探りながら、スマートファクトリー展に出展したアイレットの IoT エンジニアに工場 IoT の現状を聞いてみたいと思います。
アイレットはスマートファクトリー展に参加しました。
当日のイベント状況はこちら→
【目次】
・スマートファクトリーとは
・「スマートファクトリーJapan 2024 秋」に出展して
・「スマートファクトリー化」で何が今できるのか、 IoT エンジニアに聞いてみた。
スマートファクトリーとは
スマートファクトリーとは、2011年にドイツで提唱された「インダストリー4.0」という概念に端を発しています。「インダストリー4.0」は「第4次産業革命」の意味合いで、蒸気機関の発明で始まった「第1次産業革命」、電力と石油を利用することで熱と動力を得た「第2次産業革命」、そして、コンピューターの登場により技術革新が進んだ「第3次産業革命」に続く産業革命として捉えられています。
インダストリー4.0では、データや IoT の技術を活用し、ヒト、機械、その他の資源を連携させることで製造プロセスの最適化や新たなビジネスモデルの構築を実現させることが可能となります。
日本の「スマートファクトリー」については、経済産業省が2017年に発表した「スマートファクトリーロードマップ」のなかでまとめられている「第4次産業革命に対応したものづくり」という考え方が一般的です。
このロードマップでは、ものづくり現場での IoT 技術やロボットの活用などの重要性を認識しているものの、人材不足などを背景になかなかスマートファクトリー化の実現に向けて動くことのできない製造業界に向けて、その実現化のためのステップを提示しています。
スマートファクトリーロードマップで示された「スマート化レベル」と7つの目的
ロードマップの中では、スマート化に向けたステップを「スマート化レベル」で区分けして、その方向性を提示しています。
※画像は、「スマートファクトリーロードマップ 」(2017年5月)のデータを加工
また、ロードマップではスマート化の目的を7つに分けており、それぞれの目的に対してこの「スマート化レベル」を当てはめて確認することができます。
【スマート化の7つの目的】
- 品質の向上
- コスト削減
- 生産性の向上
- 製品化・量産化の期間短縮
- 人材不足・育成への対応
- 新たな付加価値の提供・提供価値の向上
- その他(リスク管理の強化
この記事では、7つの目的のうち「生産性の向上」を例にして、スマート化へ向けたステップを見ていこうと思います。
工場の IoT 化で生産性を向上させる
生産性を向上させる方法の1つとして、「設備の故障に伴う稼動停止の削減」が挙げられます。IoT の技術を取り入れることで、生産設備の稼働状況を監視し運用効率を高めることで、生産性を向上させることができます。
レベル1:データの収集・蓄積
レベル1の段階では、生産設備にセンサを取り付けモニタリングすることでデータを収集、蓄積し設備の稼働状況を見える化することが目標となります。また、異常や故障が発生した際に、早期にヒトへ通知できることも、「設備の故障に伴う稼動停止の削減」を目的にする場合は重要になります。
レベル2:データによる分析・予測(知見の体系化)
レベル2の段階では、蓄積された情報から、過去の事例を分析することで故障事例を分析し、その原因究明や対策の立案につながる知見を体系化することが目標となります。
レベル3:データによる制御・最適化
レベル3の段階では、故障の原因究明や対策検討の判断を、それまでに蓄積されたデータに基づいた知見で支援することにより、復旧の早期化と稼働停止時間の削減が目標となります。
スマート化の方向性
※画像は、「スマートファクトリーロードマップ 」(2017年5月)のデータを加工
スマートファクトリーロードマップでは、7つの目的を同時に進めていくよりも、優先順位の高い分野からスマート化を進めて行くことを推奨しています。
まずは1つの目的に対し、一部の生産ラインなどでレベル1からレベル3までを実践し、その導入効果を向上させることから初め、その後、工場全体や他拠点への展開など面的に効果を拡大していくことが望ましいとされています。
また、1つの目的で導入効果を得ることができたら、そのシステムを応用し他の目的へも展開していくことが良いでしょう。
「スマートファクトリー化」で何が今できるのか、 スマートファクトリー展に出展した IoT エンジニアに聞いてみた。
「スマートファクトリーJapan 2024 秋」が2024年9月18日(水)~9月20日(金)に東京ビッグサイトで開催されました。株式会社日刊工業新聞社が主催するこのイベントは、2月にも開催されており、年2回行なわれる大型の展示会イベントです。
期間中の東京ビッグサイトではスマートファクトリー展の他にも、
- 2024 洗浄総合展
- Japan Robot Week 2024
- Vacuum 2024 真空展
- 先端材料技術展 2024
- 高精度・難加工技術展 2024 / 表面改質展 2024
が同時開催されており、同時開催されていた会場の入場者数は3日間で4万以上と発表されております。
※会場地図の写真
出展ブースについて
スマートファクトリー展には、設備機器の稼働を見える化するソリューションをはじめ、AI を活用した異常検知やデータ分析など、工場の IoT を進めるための様々なソリューションが展示されていました。
今回、スマートファクトリー展での出展を担当した IoT エンジニアに、「スマートファクトリー化」で何が今できるのかを聞きました。
今回、説明してくれる IoT エンジニアはこの人!
土井田 篤
吉盛 浩司
スマートファクトリー展にはどのような方が来場されていましたか?
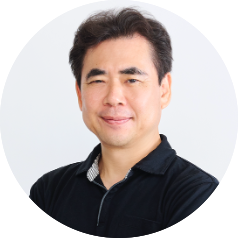
スマートファクトリー展での展示では、どのようなところに興味を持たれていましたか?
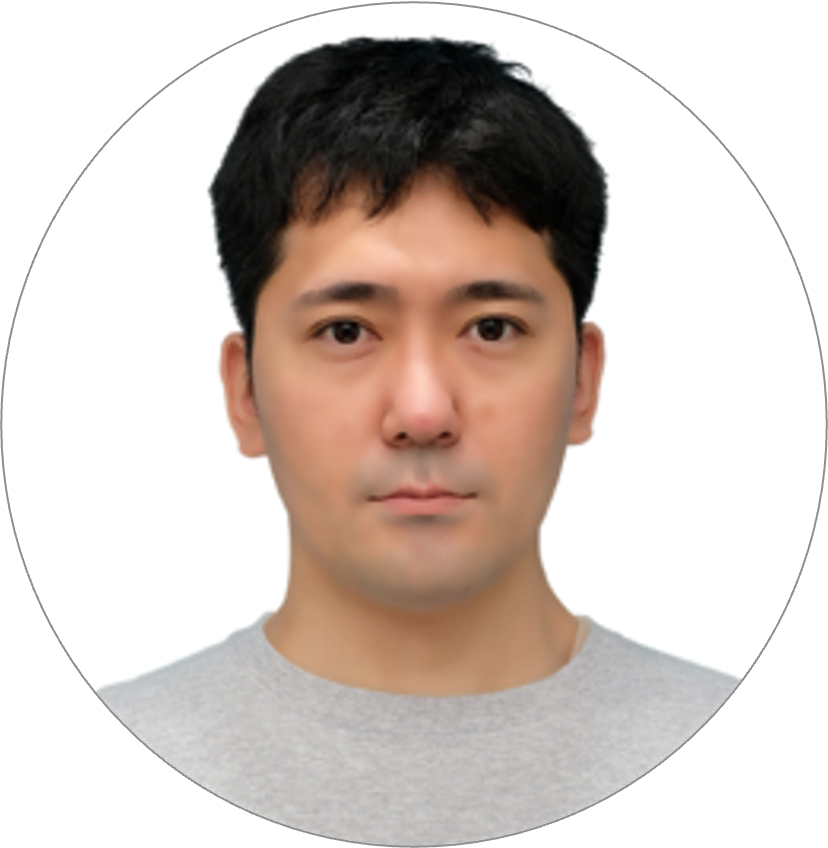
「生産設備で圧力等のデータを測定して活用したい」
「設備の稼働状況を見える化したい」
「設備の予兆保全をしたい」
「手作業でやっている外観検査を効率化したい」
「チョコ停*の原因を分析したい」
というような、具体的な課題を抱えていらっしゃる方などに多く立ち寄っていただき、お話を聞くことができました。
*チョコ停:生産設備がわずかな間だけ停止してしてしまうこと。
今回の工場 IoT の技術は、製造の流れの中の、様々な場面で活用できるのですか?
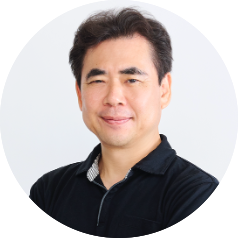
展示ではどのような点が注目されていましたか?
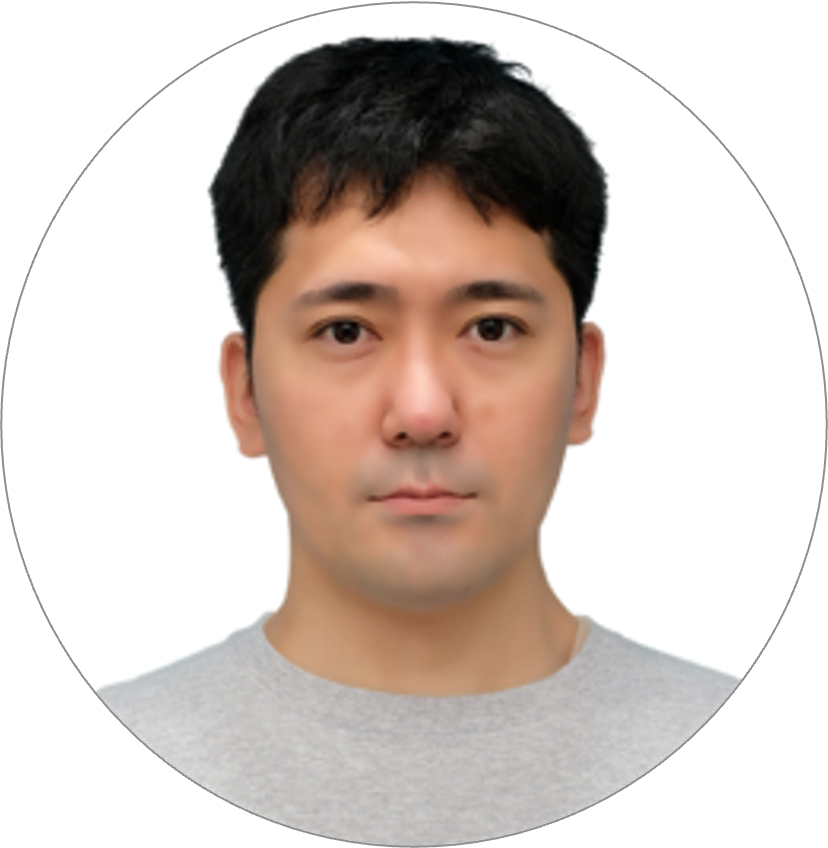
実際、トレーサビリティの機能ではどのようなことができるのですか?
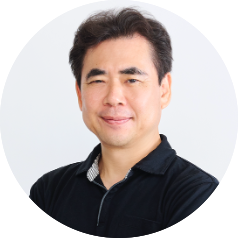
これまでトレーサビリティの実現が難しかったのには、どのような理由があるのですか?
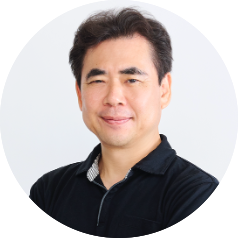
今回は、ロボットが上げてくるデータに条件を設定して、工程の開始・終了を自動的に判定できるようにしています。また、その工程のデータを製品に紐づけていく仕組みも実現しました。
今回の工場 IoT ソリューションを実際の製造現場に導入する場合には、どのような課題があると考えられますか?
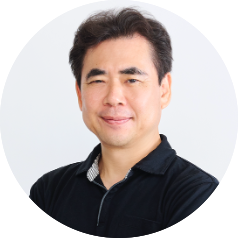
実際に製造現場に導入する際には、この条件を個々に設定していく必要があるため、そこに現場ごとの難しさがあるかもしれません。
今回の技術は今後どのように進化していくと考えていますか?
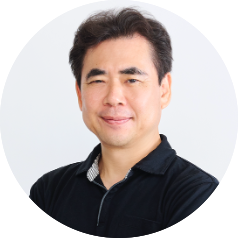
最後に、アイレットの工場 IoT ソリューションの強みを教えてください
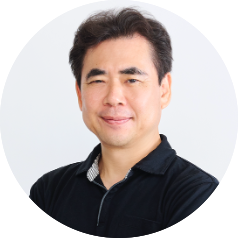
例えば、「チョコ停の原因を分析したい」というご要望であれば、機械が停止した前後の動画を表示することができたり、製品ごとの検査画像を表示させたりすることも可能です。
もちろん、インターネット上にデータがあるものであれば、既存のパッケージソフトとの連携もできるかと思います。
アイレットではお客様の工場の IoT 化やスマートファクトリー化へのご要望に対して、クラウドを活用した最適なソリューションをご提供可能です。既存のパッケージソフトでは対応できなかった機能を追加開発したいなど、スマートファクトリー導入や工場の IoT 化を加速させたいとお考えの方はぜひお気軽にお問い合わせください。
関連事例
工場設備データの“見える化”を低レイテンシ・低コストに改善し、全国拠点に展開。工場 IoT モニタリングの基盤構築
三菱マテリアル株式会社様のクラウドを活用した導入事例